Published 12 August 2024
After an investigation into Additive Manufacturing (3D-printing) identified the process could offer the UK Armed Forces significant benefits, Project TAMPA was born. DE&S joined the UK StratComm Defence Support sponsorship team to encourage industry to explore this exciting space.
Share this story
Picture the scene. The UK Armed Forces and our allies are engaged in a global conflict that is raging on land, at sea and in the air.
Quite apart from our cyber and digital capabilities, the importance of our world-leading platforms such as the aircraft carriers, armoured vehicles and fighter jets are proving just how critical they still are to providing the battle-winning edge over our adversaries.
Such is the ferocity of battle, the need for spare parts is endless. But thankfully, our Armed Forces and allies have access to global hubs where quality parts can be 3D-printed and rapidly dispatched, or even designs securely transmitted directly to users on platforms who have the technology to print them there and then.
Charlotte Robinson, Innovation Team Lead at UK Strat Comm who is has headed up Project TAMPA since its inception in 2021, said:
“That’s the future vision. There would be a series of global hubs that can rapidly print and provide assured quality parts for us and our allies. Not only could this be crucial in terms of platform availability if we did find ourselves in a conflict but brings with it a host of other benefits including quick access to spares, reduction of the need to stockpile as well as significant cost savings and environmental benefits.”
Since 2018 there had been top-level deployable Additive Manufacturing trials run at MOD Abbey Wood in Bristol, but it wasn’t until a meeting with the US Marine Corp in – you guessed it – the American city of Tampa – that the reality of what could be achieved started to bed.
Alex Champion, who was asked to deliver the project alongside Richard Hamber at DE&S, said:
“That meeting was pivotal as we heard about a new type of contract with their latest vehicle manufacturer, that included provision of an additive manufacturing design library, so that the equipment could be repaired whilst deployed on pacific islands. Their success confirmed that additive manufacturing in the UK industrial supply chain should be our priority, before focusing on front line command adoption and Project TAMPA was created by UK Stratcom with the Future Capability Group at DE&S tasked with helping deliver the programme.”
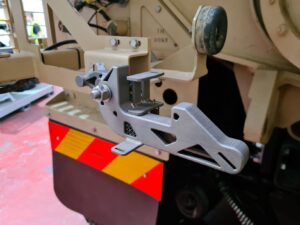
The goal for those involved in Project TAMPA was supporting industry in the Defence supply chain and giving them the confidence and expertise to adopt 3D-printing.
Charlotte said:
“We quickly identified four ‘problem areas’ that needed addressing if we were to stimulate industry in adopting Additive Manufacturing (3-D printing) at scale. Those issues were a lack of system to securely transfer print files, Intellectual Property or Design Rights, certification and qualification (of parts to ensure they’re fit for use) and robust inventory management; we set up collaborative working groups with industry to tackle these constraints in 2022 and those remain ongoing.”
DE&S set up a framework for industry and together they delivered the first challenge or ‘spiral’ which was to produce and fit metallic non-safety critical parts with Thales, Babcock, AMFG, NP Aerospace and RBSL engaged in the process.
Following this, a second ‘spiral’ was launched for metallic safety critical parts with recent events dictating that industry offering air domain or parts for Ukraine gifted platforms would be given priority consideration. This second ‘spiral’ is ongoing and is due to conclude later next year.
In tandem to the ’spirals’, the Future Capability Innovation delivery team have supported other advanced manufacturing challenges in Defence and looked at how the holistic MOD spare-part availability and supply chain obsolescence could be improved.
Alex said:
“We’ve commissioned several reports looking at spare part availability, working closely with the UK High Value Manufacturing Catapults. Additionally, we organised several Additive Manufacturing for Defence briefing days, hackathons, and other public events, to raise the awareness of the technology within MOD and more broadly across UK industry.”
Such was the success, that earlier this year Alex was brought into Defence Support, to work for Charlotte and the Project TAMPA team directly. However, DE&S continues to play an integral role as a critical stakeholder helping to stimulate industry, and encourage Defence suppliers to use additive manufacturing to supply parts in new and existing Defence contracts.
Alex said:
“We will continue to work with the DE&S project and delivery teams, to encourage them to support their parts suppliers to adopt Additive Manufacturing for equipment requiring maintenance. Additionally, we are lobbying that all future MOD purchases should include a percentage of AM parts from initial design. The opportunities are huge and it can revolutionise support to UK Armed Forces.”